Aluminum, copper, and stainless steel are among the most commonly used metals; almost any castable metal may be used including gold, titanium, and brass. Due to the smooth surface of the wax pattern that is used to create a ceramic mold, the resulting parts have a very fine finish that requires little machining. Read More…
For over 30 years, we have provided metal forged products for a wide variety of industries, including the aerospace, military, food service, medical, and automotive industries. Our customers know they can trust our forgings for quality and affordability. We will never try to make you pay more than you should for our products. Contact us by phone or email to find out more!
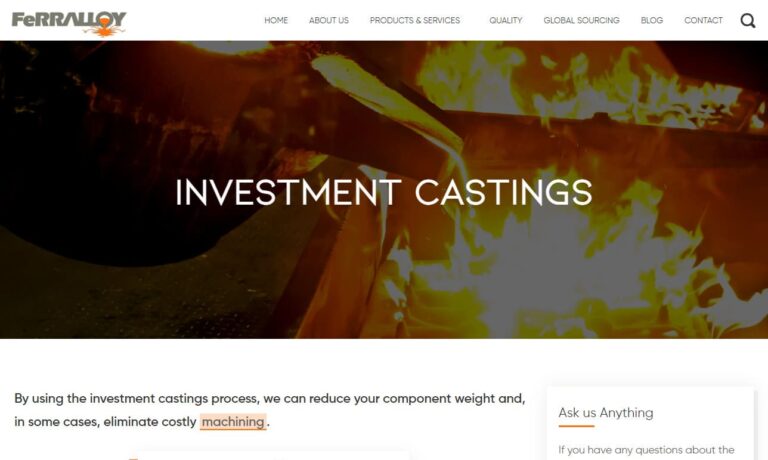
At Impro, we have top-of-the-line equipment for the most demanding investment casting requirements. Our equipment and automation process controls allow us to work with different ferrous and non-ferrous alloys, and maintain consistent and repeatable tolerances as close as ± 0.1 mm. Our investment castings are dimensionally and geometrically complex and produced to net shape, minimizing the need...
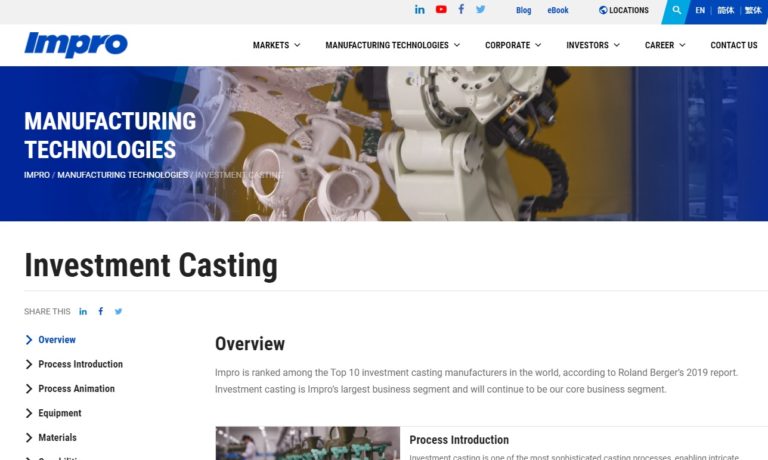
Founded in 2011, Lodestar Quality LLC is a knowledge-driven custom manufacturing solutions provider that provides manufacturers of products a full range of services from innovative design and engineering, to sourcing and production using best in class quality control methods in a cost efficient manner. Focus areas include fabrications, castings, machining and forging, plastic products, and...
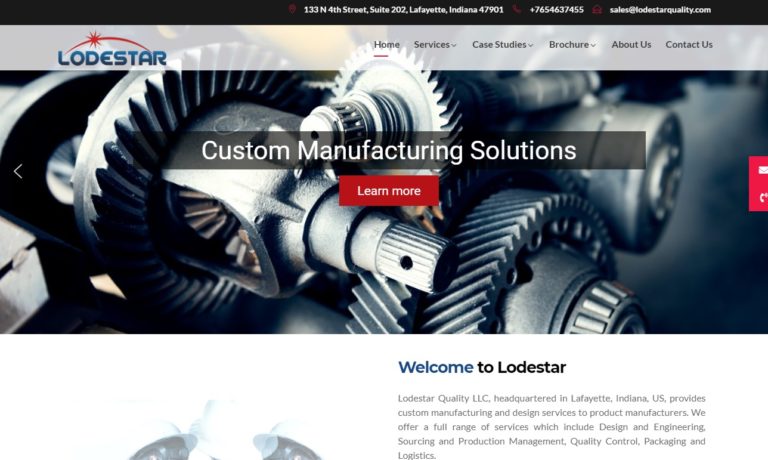
Since 1944 we have been driven to remain a cut above the competition in investment castings and everything we do. We have our own tooling shop filled with state-of-the-art testing machines. We ensure perfect results every time. It is our goal to establish lifelong relationships with our customers that benefit us both. Contact us for more info today!

At Pennsylvania Precision Cast Parts, Inc., we excel in delivering high-quality investment castings tailored to meet the diverse needs of our clients. Our expertise spans a variety of industries, allowing us to produce castings that meet precise specifications and demanding standards.
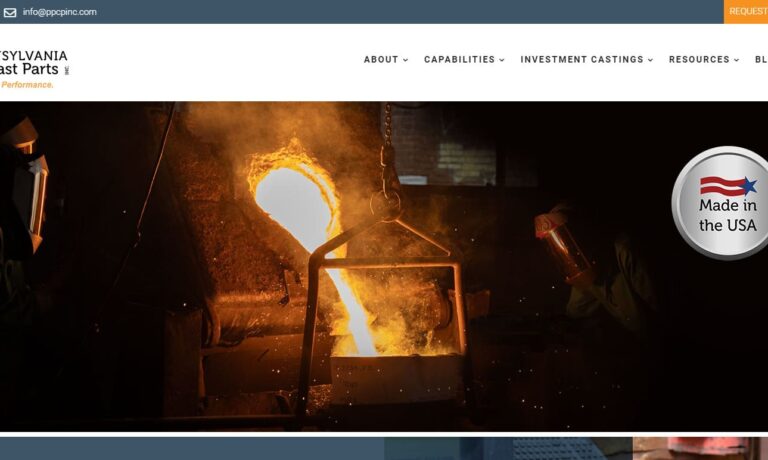
More Wax Casting Companies
Wax casting is effective at producing complex and detailed parts that other manufacturing methods cannot. There are no seams, flashes, or parting lines because the part is made as one whole piece. Because a wax model is created in the exact size and shape as the part, wax casting provides a highly accurate part. Castings can be fractions of an inch thick or weigh hundreds of pounds; most parts are around 15 pounds or less.
Wax casting is a traditional metal part manufacturing process that has been used for jewelry making for hundreds of years. It is finding modern uses in a wide variety of applications including dental and medical tools, engines, couplings, fittings, pipes, propellers, and in aerospace, automotive, dental, medical, electrical, construction, mining, food processing, telecommunication, plumbing, military, sports, and other industries.
Wax casting relies heavily on wax and its properties, though the actual wax is not necessarily pure; it may contain plastic or other substances. The wax can be carved by hand or machine but may also be produced through injection molding where hot wax is poured into a metal mold. Items such as preexisting patterns made from other materials may be covered in wax that is carefully removed when hardened then reattached.
When the wax model is ready, it is attached to a wax sprue using a heated metal tool. Depending on the size and shape of the part, several hundred patterns may be attached to the same sprue resulting in an assembly called a tree which is dipped in ceramic slurry called the investment. It is dipped multiple times in mixtures that are increasingly coarse until the investment shell is thick enough. Another method is to place the tree in a flask and pour investment into the container until the tree is completely covered.
Once the investment has hardened, the tree is inverted and placed in an oven or furnace. It is exposed to high temperatures during the burnout stage when the wax melts and runs out; all residual moisture is baked off. When removed from the oven, a liquid metal at very high temperatures is poured into the hollow shell. The metal cools within minutes and the shell can be removed, exposing the part within.